What is Lean Six Sigma in Ohio?
Contact Us
Why should you choose Six Sigma?
Six Sigma was first introduced by Motorola in 1987. The creation of this quality control methodology has been interesting since then. Its growth was slow at first, but it gradually gained traction as a result of its positive outcomes. As General Electric’s Jack Welch and AlliedSignal’s Larry Bossidy adopted Six Sigma in the mid-1990s, the technique’s early development potential was recognized. Since then, several companies all over the world have embraced and reaped the benefits of this strategy.
Six Sigma was once thought to be a “management fad” on the way to being a quality management practice! Six Sigma, on the other hand, has saved Fortune 500 companies and resulted in millions of dollars in actual earnings. As a consequence, it has shown that it is more than a management fad.
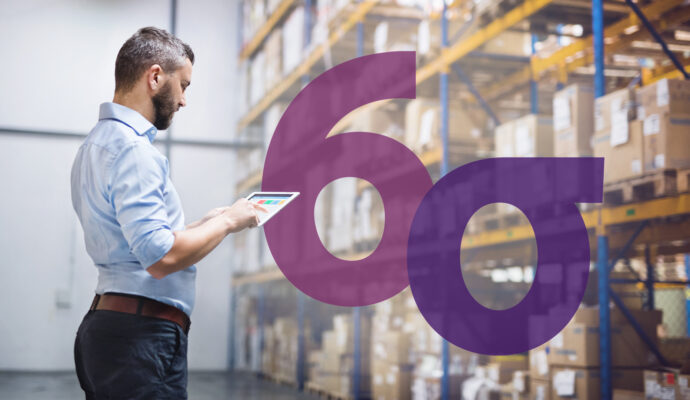
The Advantages of Using Six Sigma
The Six Sigma technique has many operational benefits when used with precision and discipline. It increases customer loyalty and retention; all long-term companies want to keep their existing customers. Clients can remain loyal to your brand whether you can maintain customer loyalty rather than switching to a new provider or product offering. Are you concerned with clients who are unhappy with your service offerings? Many companies may be oblivious of this truth, and they may be pursuing business expansion without fully comprehending their customer loyalty scores.
When you use Lean Six Sigma Experts of Ohio’s Six Sigma solution, you exclude the possibility of dissatisfied customers. We perform a market dipstick test to better explain the fundamental qualities of your service or product, which is needed for improving customer loyalty and user experience. When planning a market development strategy, we make certain that key items that can pique customer interest and help you to extend your client base, are not missed.
In today’s business climate, a unique blend of industry knowledge, performance, cutting-edge technology, and stringent quality control is needed. Do you want your company to be known as a pioneer in its field? Is gaining a competitive edge over your competitors one of your primary business objectives? Six Sigma methodologies are used to increase the productivity of accessible resources.
Frequently Asked Questions
Today's climate is on the verge of a revolution. The only exception, if there is one, is that the rate of change accelerates with each passing year. Management's position in an organization is to develop systems and value production and distribution systems for customers and company owners; this is a continuous process. To draw customers, companies must evolve to compete. Innovations change how products and services are provided to customers. Customer preferences are shifting at a breakneck rate. What appeals to you today will become a requirement tomorrow. The "transform imperative" is a philosophy that all organizations share. Organizations that aspire to be transformational leaders must change or die. Lean Six Sigma Experts of Ohio are on board with the change. We encourage continuous improvement in methodology continuity and timeliness. Management must constantly be on the lookout for new opportunities to improve their product and service offerings. Instead of being a collection of services, the operational transformation has become a way of life. Lean Six Sigma is a system as well as a set of techniques. Managers should use this as a platform to encourage creativity in their fields. Black Belts and Master Black Belts work in the organization's management and production divisions. This shows that Six Sigma is on the right trajectory and is assisting organizations in meeting their goals. When finding the right Lean Six Sigma partner, as with any other partner, vendor, or retailer, performance is critical; it seems only natural to apply a few often asked questions when evaluating prospective partners. Here are some frequently asked questions, as well as some insights into the types of answers to be expected: Your Lean Six Sigma partner should have a Six Sigma distribution and training model in place, as well as an experienced Master Black Belt on hand to support, educate, and coach on projects. The Master Black Belt should have real-world experience and be familiar with the company, economy sector, and customers' special characteristics. Candidates will build tools and apply them to real-world situations through their training. Project-based course management often necessitates the use of project result metrics, which enable learners to convert their training experiences into real-world project outcomes. This includes measuring dollars realized, process cycles, and schedule slippage, as well as implementing "toll-gates" to ensure that projects are performed on time and with high consistency. Also, the Master Black Belt can create coaching evaluations to understand and address professional and operational project problems. To make a difference, it is important to understand an organization's ability to execute a Lean Six Sigma methodology. Your partner in excellence will design activities for a readiness review and pave the groundwork for continuous deployment. This entails assessing current projects that are in the works or are in the process of being extended, as well as identifying new development indicators and initiatives. A planning evaluation should include an analysis of possible opportunities for change found in a void study, as well as a review of customer and industry survey findings. All of these components can help identify future threats, which can then be addressed. Six Sigma analyzes scenarios and evaluates results using statistical methods. Inferential statistics and probability hypotheses are used to calculate Six Sigma. Six Sigma, on the other hand, is more than just numbers. It is a set of methods for defining what the customer needs and aligning the organization and services, such as measuring systems, to fulfill those wants. Six Sigma reduces the number of complications (variation) and improves objectivity in evaluating outcomes, especially in customer delivery execution. To be a Six Sigma expert, you must have a deep passion to give outstanding customer service. The Lean method is used to eliminate waste in a systematic fashion (called Muda in Japanese). According to Taiichi Ohno, there are seven kinds of waste (TPS fame). To provide service to customers, it is important to identify and remove any waste. Both the Lean and Six Sigma methodologies are used to improve company processes and performance. Lean is more concerned with systems, optimizing processes, and improving efficiency. Six Sigma focuses on increasing performance, success, and quality.
Why Six Sigma?
How does Lean Six Sigma work?
How do you handle managing classes through their projects?
How can you incorporate your program with the work that our company is already doing?
Six Sigma is about statistics, do I need to learn statistics?
What is the difference between Six Sigma and Lean?
There are so many areas or regions where we offer these services with most of them being cities.
However, if you need any of these services, you need to contact us. The list below comprises the areas where we offer these services.